Revolutionizing Potash Mining: The Role of Fibreglass Piping in Corrosive Environments
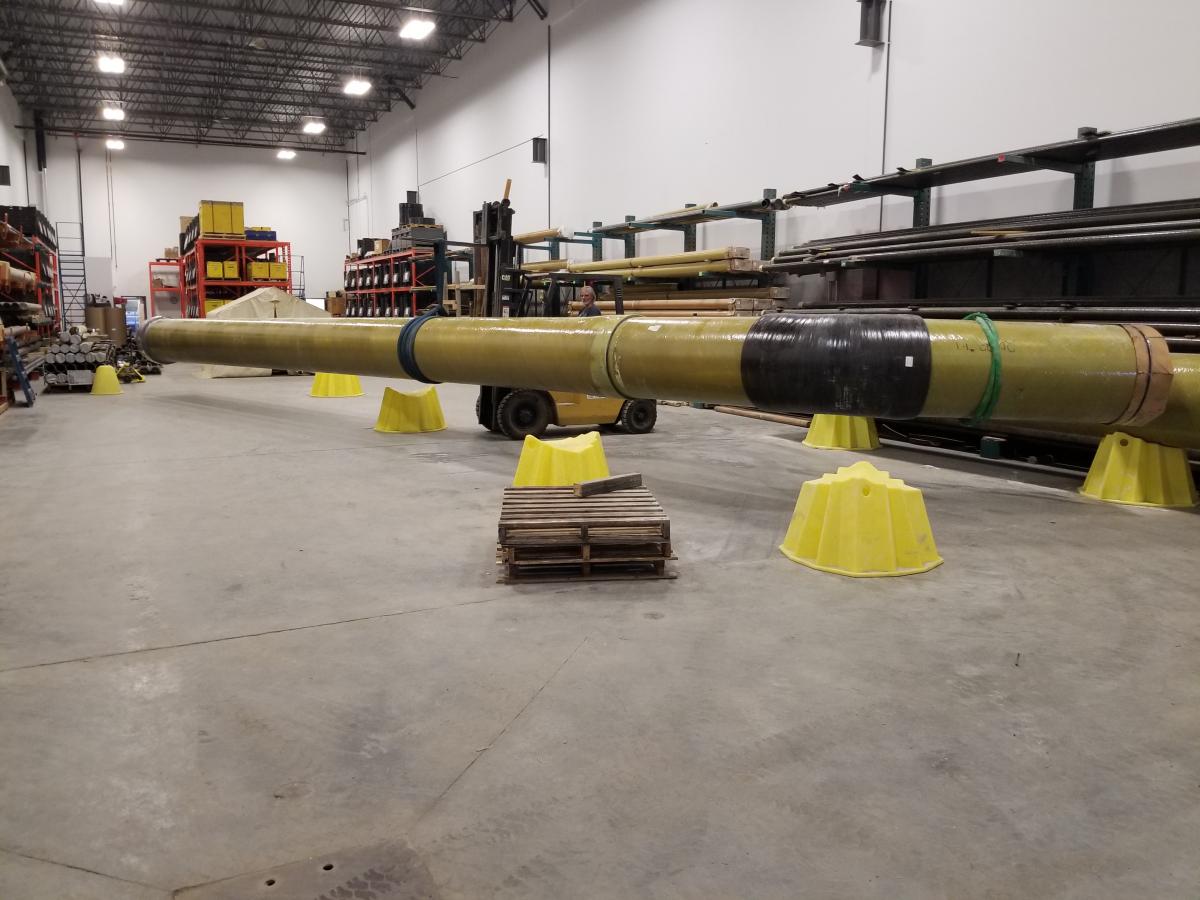
Introduction: The Growing Demand for Potash and the Challenges in Mining
Potash, a key component in fertilizers, plays a crucial role in modern agriculture by enhancing soil fertility and boosting crop yields. As the global population grows, so does the demand for potash, making its extraction and processing more critical than ever.
However, potash mining comes with its own set of challenges. The highly corrosive nature of potash brine, along with the abrasive slurry produced during processing, creates extreme conditions that traditional metal piping systems struggle to withstand. Frequent pipeline failures due to corrosion, scaling, and material degradation lead to high maintenance costs, unplanned downtime, and operational inefficiencies.
To address these issues, the industry has turned to fibreglass-reinforced plastic (FRP) piping systems, specifically glass-reinforced epoxy (GRE) pipes. These advanced piping solutions offer unparalleled corrosion resistance, durability, and efficiency, making them the preferred choice for potash mining operations worldwide.
Potash Mining Methods and the Role of Fibreglass Piping
1. Conventional Underground Mining
In conventional mining, potash is extracted using massive machines that cut into underground deposits. Once mined, the raw material is transported through pipelines where it is processed into a usable form. The challenge here is that the extracted potash comes into contact with water and chemicals that can quickly corrode traditional steel pipes, leading to frequent breakdowns. Fiberglass piping provides a solution by offering a corrosion-resistant alternative that withstands the harsh underground environment.
2. Solution Mining
Solution mining is an alternative method where water or brine is injected into underground potash beds to dissolve the mineral. The resulting solution is then pumped to the surface, where potash is extracted through evaporation and crystallization. Since this process involves continuous exposure to hot, corrosive brine, stainless and carbon steel pipes can deteriorate rapidly. GRE pipes are ideal for solution mining because they resist chemical attacks, withstand high temperatures, and require minimal maintenance.
Advantages of Fibreglass Piping in Potash Mining
1. Unmatched Corrosion Resistance
Metal piping in this service suffers from pitting, scaling, and rusting due to prolonged exposure to saline and acidic environments. Fibreglass pipes being inherently resistant to chemical corrosion, eliminate the need for expensive protective coatings or cathodic protection systems.
2. Improved Operational Efficiency and Flow Rates
One of the biggest advantages of GRE pipes is their smooth internal surface, which reduces friction and prevents mineral buildup inside the pipelines. This allows for:
- Higher flow rates with reduced pressure losses
- Lower energy consumption for pumping fluids
- Less downtime due to fewer blockages and scaling issues
3. Lightweight and Easy to Install
Compared to metal piping, fibreglass pipes are lightweight, making it easier to transport and install. This flexibility allows for quicker assembly and fewer connection points, reducing the risk of leaks. The ease of installation translates into lower labour costs during construction and faster project completion times.
4. Structural Integrity and Longevity
GRE pipes offer a high strength-to-weight ratio, allowing it to withstand:
- High operating pressures (ideal for deep underground mining)
- Extreme temperatures (essential for solution mining)
- Mechanical stress and vibration without cracking or failure
- The lifespan of fibreglass piping systems is significantly longer than metal alternatives, providing a long-term, cost-effective solution for mining operations.
5. Reduced Maintenance and Downtime
One of the major cost factors in mining operations is maintenance. Metal pipes require frequent repairs, replacements, and anti-corrosion treatments, whereas GRE pipes need minimal upkeep. This leads to:
- Lower maintenance costs over the lifespan of the pipeline
- Fewer operational interruptions
- Enhanced overall productivity
Environmental and Sustainability Benefits of FRP Piping
In addition to operational and fiscal advantages, fibreglass piping contributes to sustainable mining practices by:
- Reducing material waste – Longer-lasting pipelines mean fewer replacements and less landfill waste.
- Minimizing chemical treatments – Unlike steel pipes, FRP systems do not require toxic anti-corrosion coatings.
- Lowering carbon footprint – Lightweight materials reduce transportation and installation energy costs.
As the mining industry moves towards eco-friendly and energy-efficient solutions, FRP and GRE pipes align with sustainability goals, making them a smart investment for the future.
Check out our article, Sustainable Solutions: The Environmental Edge of FRP Piping Systems to learn more about the environmental benefits of FRP piping.
Conclusion: The Future of Fibreglass Piping in Potash Mining
As global potash demand continues to rise, mining companies must adopt durable, efficient, and cost-effective infrastructure to stay competitive. Fibreglass-reinforced plastic (FRP) and glass-reinforced epoxy (GRE) piping offer a game-changing solution by addressing the challenges of corrosion, flow efficiency, and maintenance costs.
With proven success in both conventional and solution mining, fibreglass piping is set to become the industry standard for potash transportation. Companies investing in these advanced piping systems will not only enhance their operational efficiency but also contribute to a more sustainable and resilient mining industry.
To learn more about the application of fibreglass-reinforced plastic piping in various industries contact us.