Advancing Energy Efficiency with Fibreglass-Reinforced Plastic (FRP) Piping
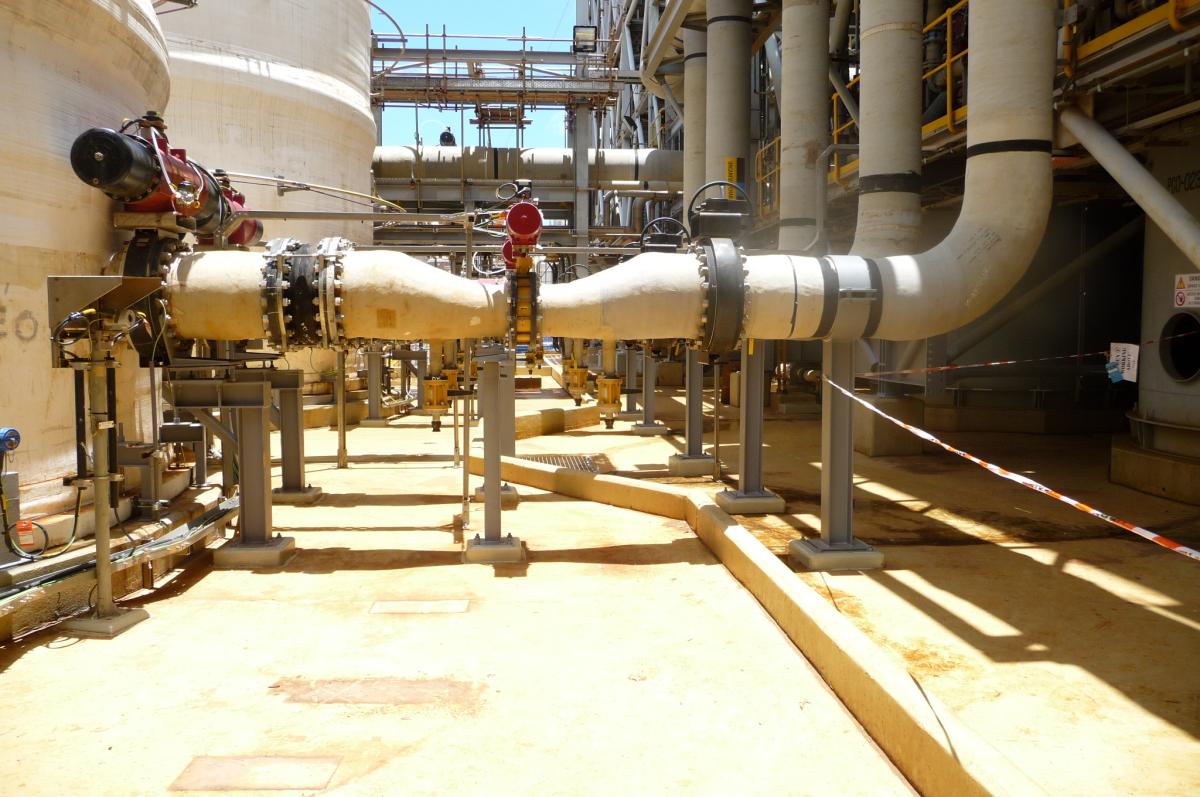
Worldwide, the pursuit of energy-efficient and sustainable operating practices is relentless. Fibreglass-reinforced plastic (FRP) piping emerges as a game-changer in this quest, offering a blend of strength, durability, and corrosion resistance unmatched by traditional materials. This blog explores the transformative impact of fiberglass piping on energy efficiency within the conventional and in-situ oil sands sector, illustrating why it's becoming an indispensable component of modern facility infrastructure.
The Rise of Fibreglass Piping in Conventional and In-Situ Oil Sands
The emergence of Fiberglass-reinforced plastic (FRP) piping as a pivotal material in conventional and in-situ oil sands operations represents a transformative move towards operational efficiency and environmental stewardship. Initially introduced as an innovative substitute for steel and concrete piping, Fiberglass piping continues to establish itself as a frontrunner in the sector due to its exceptional adaptability to the demanding and varied conditions of hydrocarbon extraction and processing applications.
Fibreglass-reinforced plastic piping has a distinct composition, which integrates a durable polymer matrix with robust glass reinforcement, providing extraordinary capabilities to withstand the industry's inherent challenges. This includes exceptional resistance to corrosive substances, abrasive fluids, and the wide range of pressures and temperatures typical in energy facilities. The material's resilience against such aggressive conditions not only extends the lifespan of piping systems but also reduces the frequency and cost of maintenance and replacements.
Furthermore, fiberglass piping’s introduction into the conventional and in-situ oil sands sector has catalyzed a shift in material engineering and design philosophies. Engineers and designers now have the flexibility to create more tailored and efficient piping systems that leverage fiberglass's unique properties, such as its lightweight nature and ease of installation. This adaptability is proving crucial in operations, where the logistical challenges of transporting and installing piping can significantly impact project timelines and costs.
Enhancing Energy Efficiency with Fibreglass
Glass-reinforced plastic (GRP) piping is revolutionizing conventional and in-situ oil sands operations' approach to energy efficiency. The material's lightweight characteristics play a pivotal role in reducing the energy consumed during the transport and installation phases, leading to lower greenhouse gas emissions and decreased operational expenses. This advantage is particularly significant in remote locations where logistical challenges can amplify costs and environmental impacts.
Additionally, the inherent smoothness of FRP's internal surfaces dramatically enhances fluid dynamics, minimizing resistance and thereby lowering the energy demands of pumping operations.
This efficiency in fluid transport not only conserves energy but also enables systems to operate at optimal levels with less wear and tear, further extending the lifespan of the infrastructure.
The combination of these features—reduced weight, improved flow efficiency, and exceptional durability—positions FRP as a key contributor to conventional and in-situ oil sands operations' efforts to minimize energy consumption. By requiring less energy for both operational and maintenance activities, fiberglass systems significantly diminish the industry's overall energy footprint, aligning with global initiatives aimed at reducing energy use and promoting sustainability in industrial processes.
Operational Benefits and Applications
Glass-reinforced epoxy (GRE) piping offers a multitude of operational benefits that extend well beyond its contribution to energy efficiency. One of the most significant advantages is its exceptional resistance to corrosion, invaluable in the harsh environments typical of conventional and in-situ oil sands operations. This resistance to degradation ensures that fiberglass systems have a longer operational life, reducing the likelihood of leaks, failures, and the associated costly downtimes.
Moreover, the inherent durability and reliability of fiberglass minimize operational disruptions, thereby enhancing the overall efficiency and safety of operations. The material's resilience leads to fewer unexpected maintenance issues, allowing for smoother and more predictable operations.
GRE’s versatility further broadens its application within the industry. It is adeptly used in a variety of settings, from production lines, where it transports oil sands from extraction points to processing facilities, to injection systems that require the conveyance of water or chemicals into wells for enhanced recovery. Additionally, fiberglass is utilized in cooling water circuits, essential for maintaining optimal temperatures in processing equipment. This wide range of applications underscores FRP's adaptability and its role in improving operational performance across the conventional and in-situ oil sands value chain.
Economic and Environmental Impact
Integrating Fibreglass-reinforced plastic (FRP) piping into conventional and in-situ oil sands operations significantly influences both economic and environmental aspects. Economically, fibreglass presents a dual advantage: it not only reduces the direct operational costs associated with maintenance and repair but also lowers the capital expenditures required throughout the project's lifecycle. The inherent durability and minimal maintenance needs of fiberglass mean that systems last longer without the need for frequent overhauls or replacements, translating into direct cost savings and improved asset utilization for operators.
From an environmental perspective, the benefits of adopting fiberglass are equally notable. The production process of FRP is inherently more energy-efficient and generates fewer carbon emissions than the manufacture of traditional materials like steel or concrete. This reduced carbon footprint aligns with the growing emphasis on sustainable practices within the industry.
Furthermore, the longevity and efficiency of fiberglass piping systems mean that less energy is consumed, and fewer resources are needed over time, contributing to a reduction in the overall environmental impact of conventional and in-situ oil sands operations.
Moreover, FRP's resistance to corrosion and chemical degradation reduces the likelihood of leaks and spills, further safeguarding the environment from potential contamination associated with pipeline failures. This aspect of fibreglass not only supports the industry's sustainability objectives but also helps in complying with stringent environmental regulations, reinforcing fibreglass’s role in fostering more responsible and sustainable conventional and in-situ oil sands operations.
Conclusion
As conventional and in-situ oil sands operations continue to confront the dual challenges of meeting global energy demands and reducing their environmental footprint, Fibreglass-Reinforced Piping stands out as a critical ally. By advancing energy efficiency, reducing operational costs, and mitigating environmental impacts, fibreglass is not just a material of choice but a strategic asset in the future of conventional and in-situ oil sands operations. Its growing adoption is a testament to the industry's commitment to innovation and sustainability, paving the way for a more efficient and responsible energy landscape.
Interested in exploring how Fibreglass-Reinforced Plastic Piping can enhance your operations?
Contact Us today to learn more about our solutions and how we can assist you in achieving your efficiency and sustainability goals.